
RISK DETECTION
OF THE FUTURE
Our Products – Dynamic Risk Analyzer® (DRA), Batch DRA™, and ARC DRA™ – identify hidden process risks autonomously for continuous, batch, and semi-continuous processes using our proprietary machine learning technology.
DYNAMIC RISK ANALYZER (DRA)
Dynamic Risk Analyzer® (DRA) is a first-of-its-kind early risk detection and advanced warning software that identifies process problems at initiation stage – enabling operating personnel to take proactive corrective actions and prevent losses.

Simple. Powerful.
One Platform to Detect All.
Dynamic Risk Analyzer™ (DRA) has been proven to improve uptime, safety, and reliability in industrial plant operations. It delivers actionable, early indicators of process issues – typically days and weeks before the alarms go off. What makes it unique is our distinctive, patented approach of identifying hidden near-misses™ (early indicators) in the process data. This enables the operating teams to avert problems just when they are beginning to form, to plan predictive maintenance, and to achieve ultimate safety and bottom line.

ANOMALY DETECTION
Find the anomalies before they find you. Our powerful algorithms work rigorously to identify conditions that are not normal and can pose problems in the future.

HIDDEN TREND DETECTION
Transform how you assess risks in your operations. Discover hidden process issues, equipment issues, instrumentation issues, operator issues and many more.

PLUG AND PLAY
Easy, quick installation. Built to be plug and play with your existing systems.
PROCESS INTELLIGENCE
Besides risk and anomaly detection, access process intelligence insights to make proactive, operating decisions.
RISK COMMUNICATION
Modern communication tools at your fingertips. Messaging, blogging, reporting, you name it.
DATA PRIVACY
All the results stay within your network. No export of data outside your facility. This way your expertise remains in-house.
BATCHDRA
BatchDRA™ is a software designed for early risk detection, providing unparalleled insights into the dynamics of batch processes. Its primary objective is to autonomously identify potential problems at an early stage. Equipped with this critical information, the operating team can swiftly take proactive steps to address these issues. Furthermore, it enables the team not only to mitigate risks but also to enhance the efficiency of batch cycles. The result is a significant increase in both productivity and profitability.

AUTONOMOUS AI AND MACHINE LEARNING TECHNOLOGY
No dependency on expert skills for risk identification, process changes are integrated automatically
PLUG AND PLAY WITH 1-DAY INSTALLATION
No model building or pre-determined signatures required
EASY TO SCALE TO MULTIPLE PRODUCTS AND PLANTS
Covers the entire product line, easy integration with other software
EXCELLENT KNOWLEDGE MANAGEMENT
Helps to capture employee knowledge and retain a library of process highlights
Our Technology Milestones
2015
DRA LAUNCHED
FIRST INSTALLATION OF DRA AT CUSTOMER SITE
2019
FAULT TREES (NEW DRA MODULE) LAUNCHED
2020
SLOPING TREND (NEW DRA MODULE) LAUNCHED
2021
OPERATING FITNESS (NEW DRA MODULE) LAUNCHED
2022
REAL-TIME (NEW DRA MODULE) LAUNCHED
2023
BATCH DRA (NEW PRODUCT) LAUNCHED
2024
ARC DRA (NEW PRODUCT) LAUNCHED
How It Works
Risk Detection using Autonomous Machine Learning
A typical industrial plant has 2,000 – 5,000 parameters, continuously recording sensor measurements that generate millions of data points every day. Powered by our patented technology, centered on autonomous machine learning, DRA scans the entire spectrum of process data and identifies critical anomalies (also called hidden near-misses™), which are precursors of potential failures. This information on developing risks is available to all levels of your operations team, including managers, supervisors, engineers, operators, and maintenance team. The result: operational transparency, proactive risk management driven workflow, and effective communication.
​
Data source connectivity is seamless and no new IT infrastructure setups are required for the installation. DRA server sits within your secured network and receives data automatically via your existing historian, OPC, or similar systems. All standard data sources (such as Aveva PI, Aspen IP21, DataPARC, Yokogawa Exaquantum, Honeywell PHD, etc.) are supported.
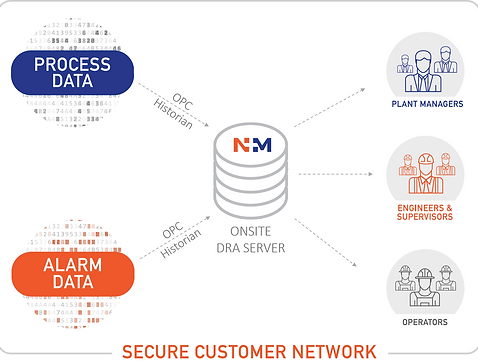
WHAT OUR CUSTOMERS ARE SAYING
“During the first full year implementation of DRA, production losses were reduced from 3.5 cargoes (2018) to 0.4 cargo (2019) => 3.1 cargoes gain.”
Area Manager, LNG